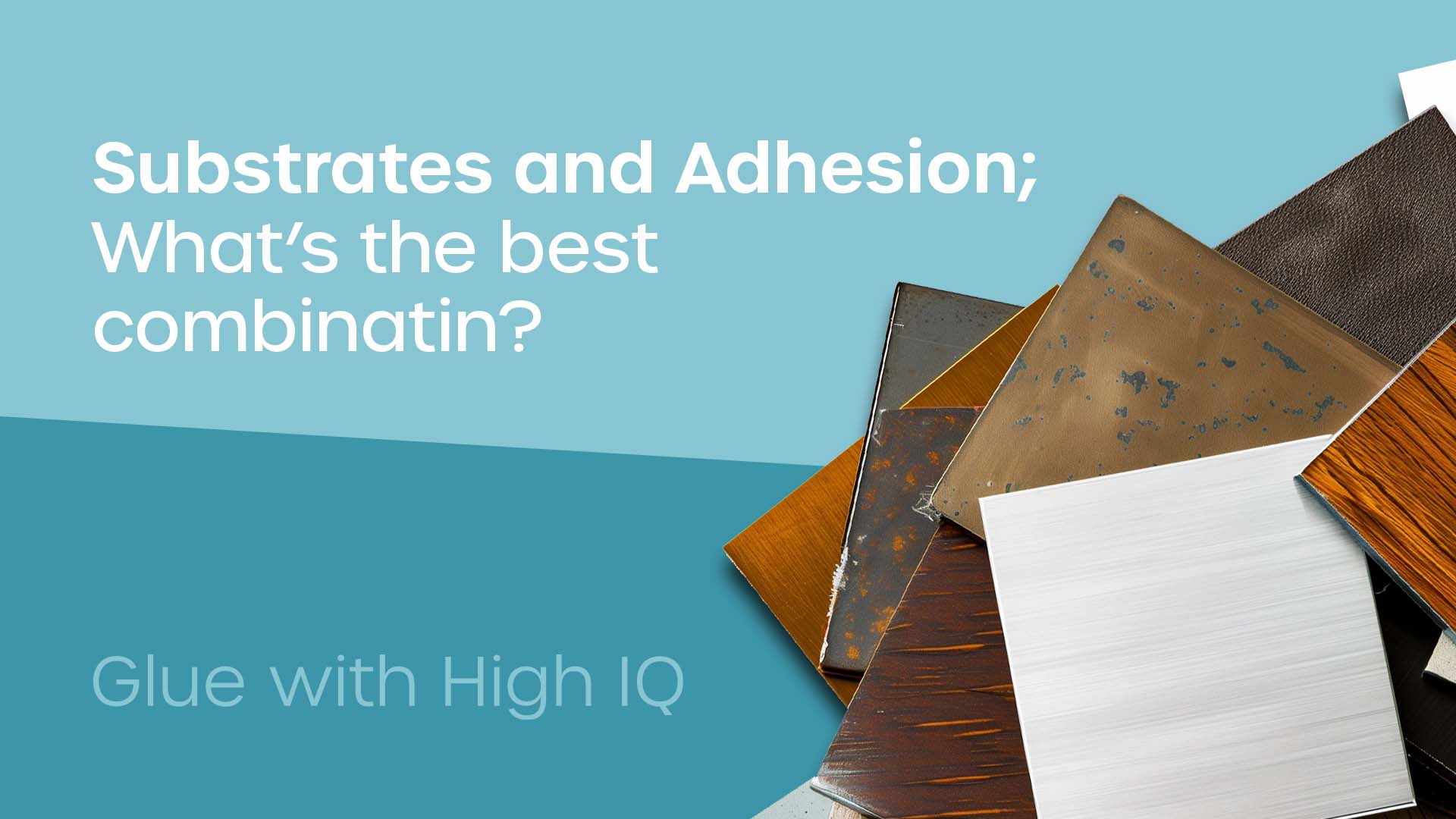
There are many things to consider when selecting your substrate. The composition, metals (which contain a layer of oxides and gases), or non-mentals (which contain moisture and additives). In this blog, we’ll be covering different types of substrates and their individual properties to help you make an informed decision.
Powder Coated Metals
The treatment of powder coating reduces a metal’s chance of corrosion and degradation, but also reduces the surface tension, deeming it less desirable for adhesive bonding.
The process of powder coating uses a free-flowing powder to coat the surface of a metal substrate through an electrostatic charge. It is then baked until a hard exterior is formed. Powder coating is used over liquid paint due to it’s characteristic to form a ‘hard skin’, for it’s non-drip and non-sag properties and for even coat weights.
There are very few problems associated with powder coated substrates. However, in some cases, powder coat powders can be applied to substrates with uneven coat weights (a thicker build up in some areas and a thinner layer in others), causing intermittent adhesion to occur. Not only this, if only one side of a metal is to be coated, over-spray can occur on the reverse side of the metal; also causing intermittent adhesion over the areas where the over-spray has formed.
EPDM Rubbers
EPDM rubbers are notoriously hard to bond to, due to their high composition in butadiene and styrene. Not only do these two compounds reduce the surface tension, but they can also cause yellowing and de-bonding of the adhesive as a result of styrene leeching out of the rubber.
Porous Substrates
A substrate which is porous in nature has a reduced surface area for bonding. When bonding an adhesive to a porous substrate, it is likely that there will be air entrapment or moisture underneath the adhesive if the correct precautions are not taken. With an insufficient surface area and air pushing against the adhesive, it is almost certain that the adhesive will de-bond, showing thin film adhesion or adhesive failure.
Amorphous Thermoplastics
Stress cracking can occur on amorphous plastic materials when subjected to two different environments:
- In contact with solvents, breaking down the structure of the plastics causing cracks to form.
- Environmental stress corrosion cracking; repeated tensile stress stretching the thermoplastic inducing cracks.
The plastics which are more susceptible to stress cracking are:
- Polycarbonates
- Polymethyl methacrylates (PMMA)
- Polystyrene
- Acrylics
- Styrene-acrylonitrile
- Polysulfone
- ABS
- Polyphenylene oxide
What affects surface cracking?
- Time
- Temperature
- Solvents
- Plastic type
- Adhesive type
- Force applied
- Environment
- Surface preparation methods
Ways to prevent stress cracking:
- Use adhesives which are free from solvents
- When joining materials together, avoid stretching or deforming the plastic as this can generate stress from the outside
- Post bake plastic parts to reduce internal stresses
- When using solvent-based adhesives, ensure that the curing time is fast to minimize the length of time the solvents are in contact with the plastic
- Do not over apply solvent based adhesives to plastic materials
- Do not leave adhesive residues on the edges of joints
- When using UV curable adhesives, ensure the adhesive is cured immediately after application
- Anaerobic adhesive should not be used to join amorphous thermoplastics
- Prepare thermoplastic surface with the use of abrasion and cleaning with IPA
If you’re unsure about any of the above, or would like some advice, feel free to contact our specialists on the number above.
Topics: